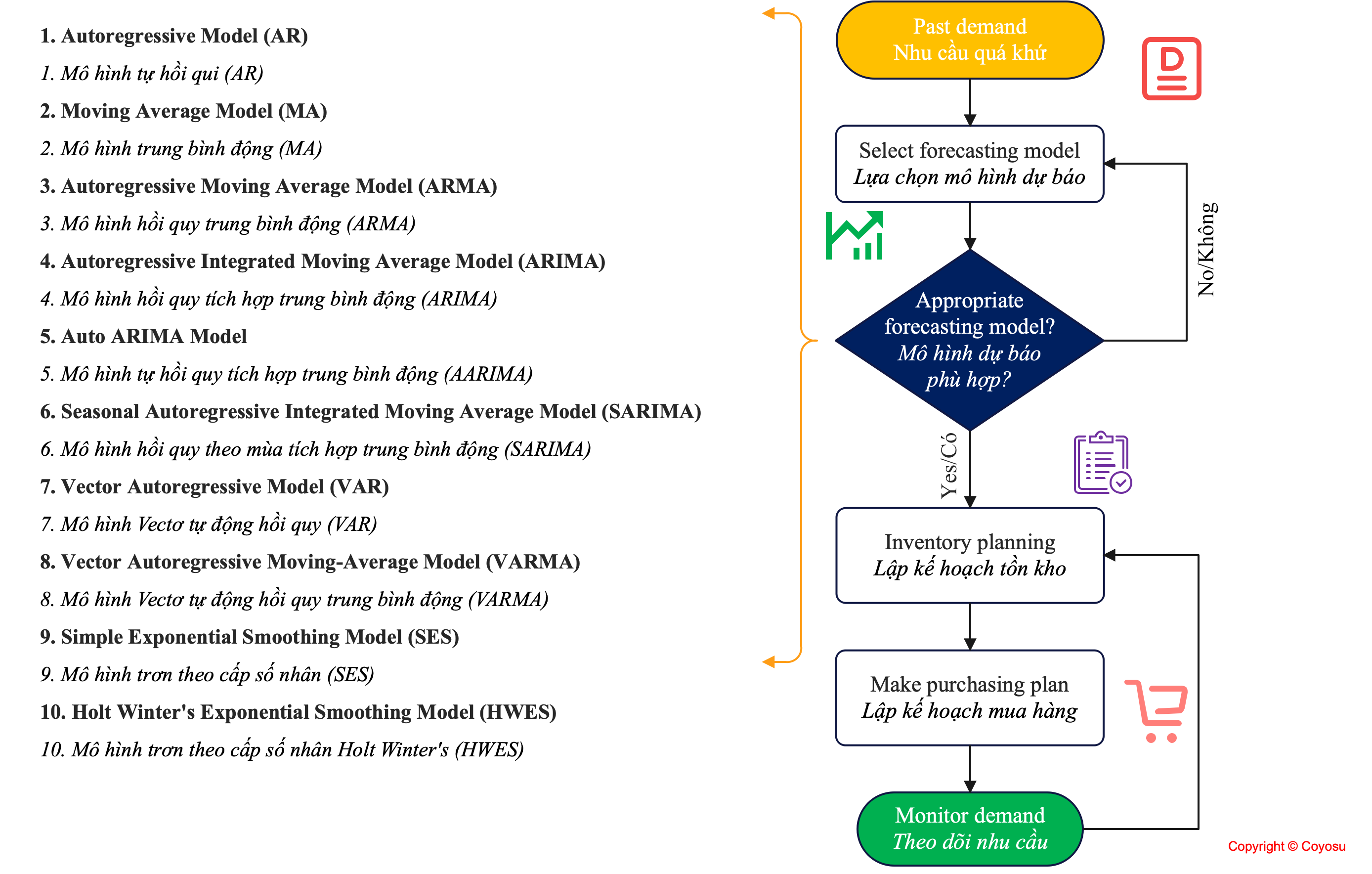
FORECASTING
Because the purchasing time is long and customers cannot wait any longer, spare parts for maintenance and repair are extremely important as follows:
Increase customer service levels while maintaining appropriate inventory levels.
Have a suitable purchasing plan for each time.
Reduce spare parts inventory levels.
Reduce storage costs.
Manage cash flow to buy spare parts more appropriately.
With 10 popular forecasting models, it helps companies choose a forecasting model that suits market needs.
10 FORECASTING MODELS
1. Autoregressive Model (AR).
2. Moving Average Model (MA).
3. Autoregressive Moving Average Model (ARMA).
4. Autoregressive Integrated Moving Average Model (ARIMA).
5. Auto ARIMA Model.
6. Seasonal Autoregressive Integrated Moving Average Model (SARIMA).
7. Vector Autoregressive Model (VAR).
8. Vector Autoregressive Moving-Average Model (VARMA).
9. Simple Exponential Smoothing Model (SES).
10. Holt Winter's Exponential Smoothing Model (HWES).
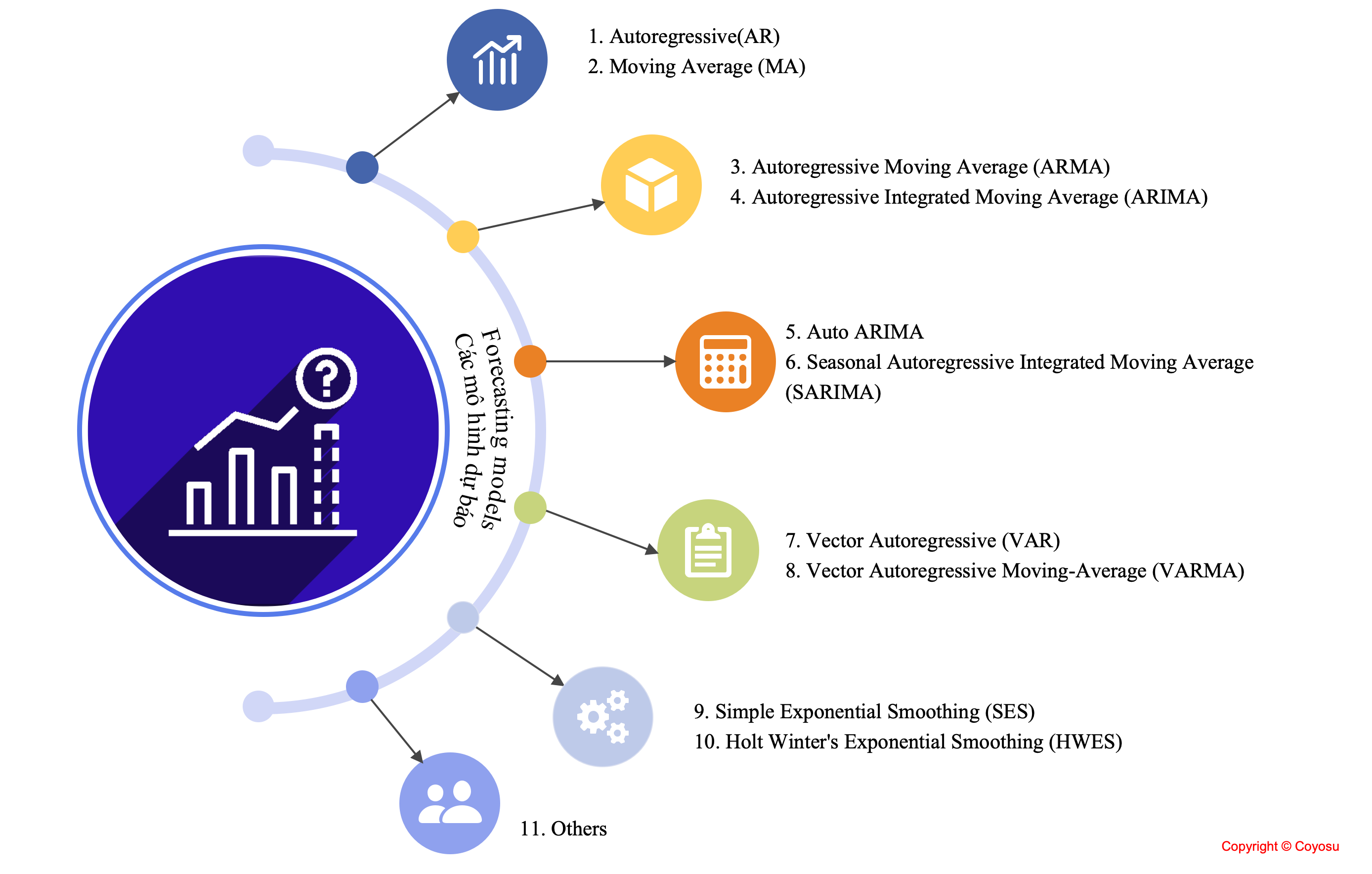
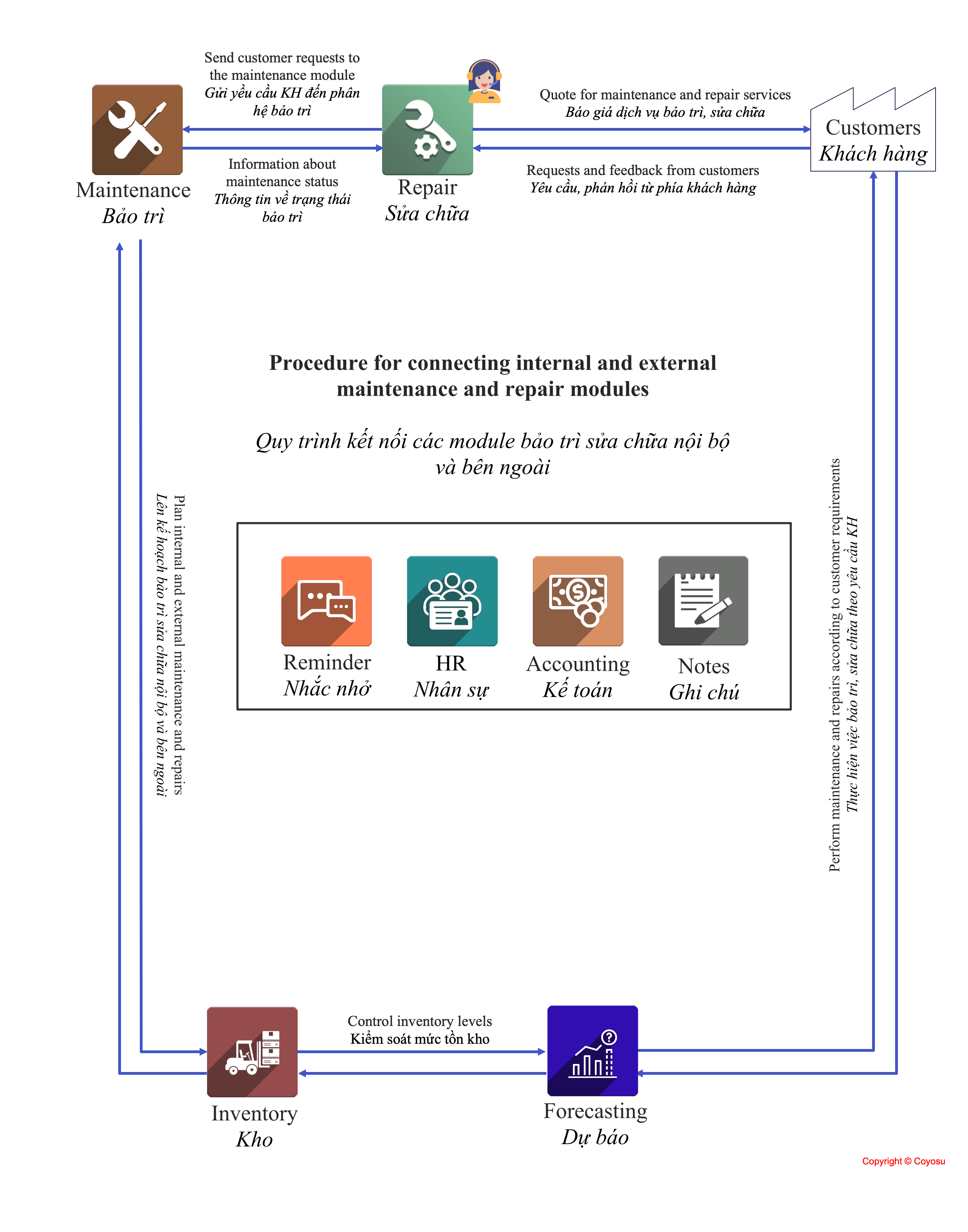
FEATURES
CASE: INTERNAL MAINTENANCE AND REPAIR
Manage the list of equipment and spare parts that need repair.
Manage equipment and spare parts details including: catalog, video, supplier, supplier code, model, serial number, warranty, maintenance and repair schedule, frequency of preventive maintenance, team maintenance, technicians are responsible for each device, spare part...
Plan maintenance, repair and preventive maintenance.
Assign tasks to each maintenance staff.
Checklist of detailed maintenance and repair work.
Connect, chat and work as a team, record work exchange history.
Remind maintenance and repair work until it is completed, otherwise the system will switch to overdue state (so maintenance staff never forget their work).
You can review previous maintenance notes to make repair and maintenance work faster.
CASE: MAINTENANCE AND REPAIR SERVICES
Quote for services and repair parts
When the customer agrees, link with the internal maintenance team to plan maintenance and repairs for the customer.
Assign tasks to each maintenance staff and provide work reminders.
Checklist of detailed maintenance and repair work.
Manage reasons why repair quotes failed.
Create invoices if accounting module is added.
BENEFITS
FOR MANAGERS
Know the reason why the repair quote fails and then have better solutions.
Know the late maintenance and repair work and who undertakes this work.
Assign work to employees.
Receive support requests from maintenance staff.
Work exchange history is stored so the level of interaction of all employees can be clearly seen.
FOR MAINTENANCE STAFF
Tasks are reminded by the system so they cannot be forgotten.
Create a work checklist to perform work without errors.
Information is concentrated in one place so you don't have to worry about doing the job incorrectly or without needing to ask anyone.
Difficulties can be sent to management for immediate support.
Group interaction to support faster and better work performance.
Don't waste much time reviewing device parameters and notes when repairing because the system has stored information on each device.
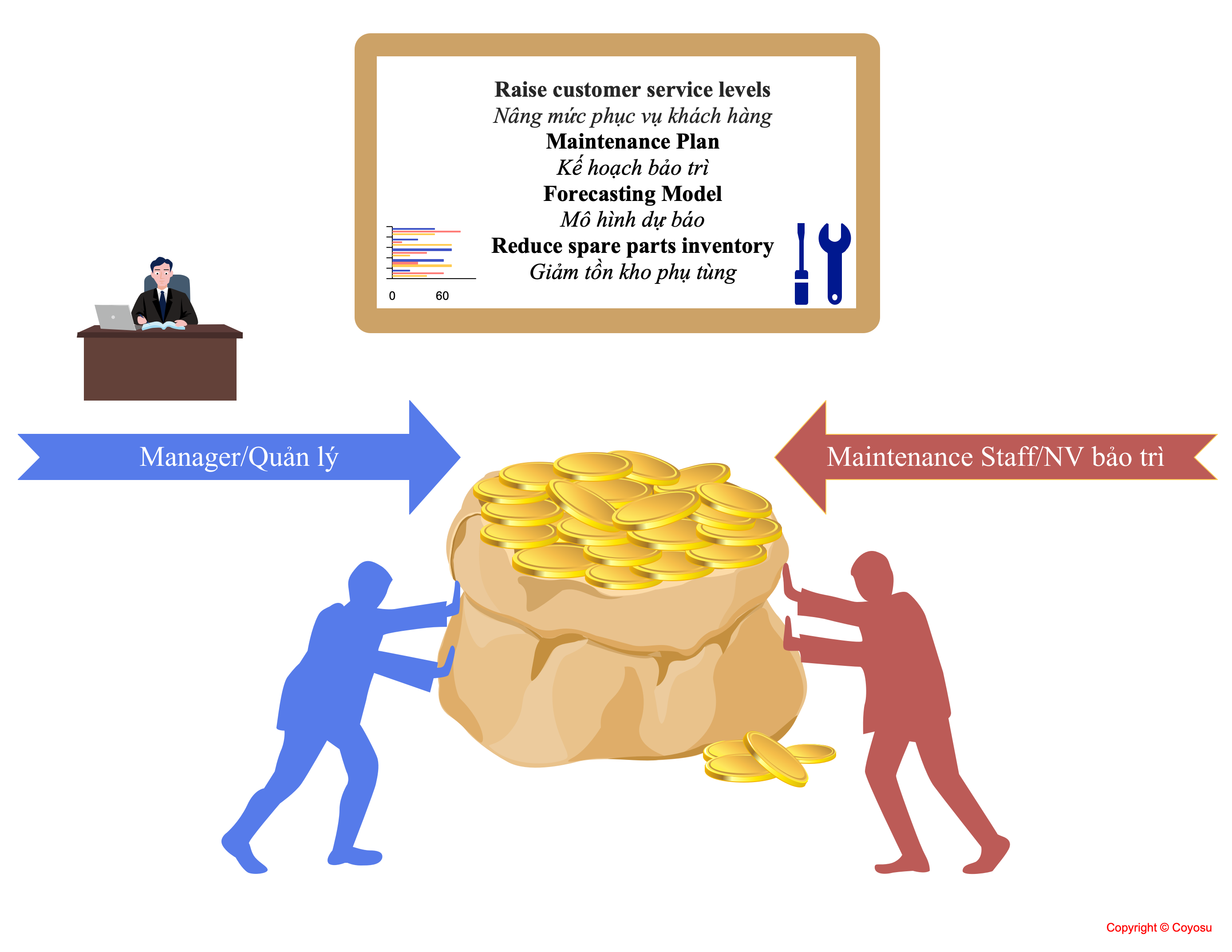
If you have any questions please feel free to contact us!